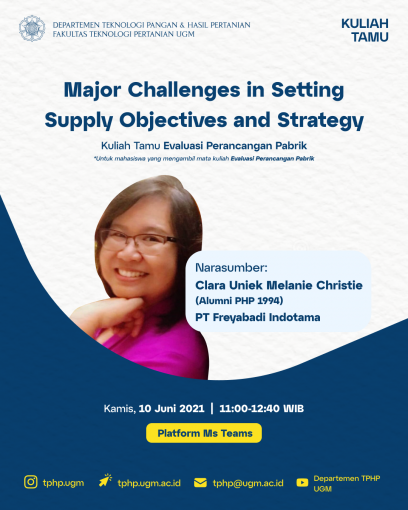
On Thursday, June 10, 2021, the TPHP UGM Factory Design Evaluation course held a guest lecture with the theme “Major Challenges in Setting Supply Objectives and Strategy”. This guest lecture was presented by Clara Uniek Melanie Christie from PT Freyabadi Indotama and hosted by Dr.nat.techn. FMC Sigit Setyabudi, S.T.P., M.P., TPHP UGM lecturer. The guest lecture, which took place at 11:00-12:40 WIB, was conducted through the Ms. Teams platform and attended by 112 participants.
The supply chain is a network between a company and its suppliers to produce and distribute certain products to customers. This network usually includes customer orders, PPIC, purchasing, production, and distribution. It needs to be maintained by providing the flow of materials, supplies, and services as required by customers.
The supply chain is a network full of uncertainty so inventory management is needed to determine the right level of inventory. Too much inventory will make the money spent by a company die in working capital due to the high cost of storing goods and operational costs in the warehouse, but too little inventory can also result in stockouts (lack of raw materials) so that later it will make the company’s customers disappointed. To avoid these things, it is necessary to hold buffer stock in inventory management.
Buffer stock or safety stock is inventory that is usually prepared by a company by exceeding the amount of stock of an item in the warehouse to anticipate a stock out (lack of raw materials or goods). Stock out usually arises because customer demand is too high and unpredictable when it comes to demand for an item. Buffer stock must be controlled or managed properly, be it stock for raw materials or stock for finished goods.
3 things must be considered in calculating buffer stock, namely demand variation, lead time, and service level. Customer demand for a product always varies or is not constant so the variation in demand must be directly proportional to the buffer stock so that the chance of stock-outs will be small. Lead time is the duration of time when the company orders an item until the item reaches the hands of the orderer. The longer the lead time listed, the greater the buffer stock that must be prepared so that when demand for goods unexpectedly increases, at least the company already has more stock for the demand. Service level needs to be determined by each company and how much they can provide to each customer. The greater the service level provided to customers, the greater the buffer stock that the company must prepare.
Continuity of supply needs to be done so that the supply chain can continue to rotate as it should. Several factors need to be considered when conducting supply continuity, including self-production or purchase from other industries, material quality (standard/special), source (local/regional, one/more suppliers), supply method (blanket order/bid/contract), and use of substitute materials. However, the use of substitute ingredients must be carefully considered because it will affect product specifications (nutrition facts and labeling claims), ingredient handling, production process, and the cost required for the overall process.
“Sustainability focuses on meeting the needs of the present without compromising the ability of future generations to meet their needs so that it is hoped that the current ingredients will remain for generations to come,” said Ms. Uniek. The concept of sustainability consists of three pillars: economic, environmental, and social – also known informally as profit, planet, and people.
The video of the Factory Design Evaluation Guest Lecture can be accessed through the following link