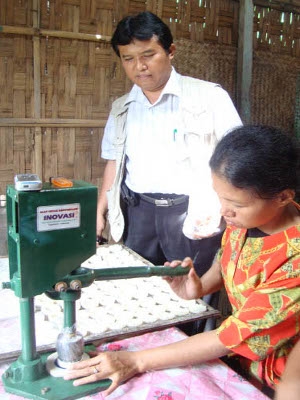
For those of you who like light snacks, you must be familiar with the name rengginang. This glutinous rice snack is still favored by the public. However, who would have thought that the process of making rengginang requires a lot of care and skill? So far, the process of molding rengginang is still done manually, without the use of special printing equipment. In addition to taking a long time, the manual molding process only produces rengginang in low capacity.
Seeing this problem, Ir. Priyanto Triwitono, MP. a lecturer in the department of Agricultural Product Processing Technology (TPHP) of FTP UGM was moved to find a solution to overcome the problem of efficiency and productivity of making rengginang by developing a rengginang printer.
Priyanto said the idea to make a rengginang printer started when he gave counseling to a group of small and medium enterprises (SMEs) at the Yogyakarta Agriculture Office in 2003. One of the SMEs that made rengginang complained that it was difficult to print rengginang manually because it requires a lot of skill and the production capacity is low. “Orders were pouring in from various regions, but they couldn’t fulfill all the orders because the printing process could not be done quickly and in large quantities,” he explained recently.
The rengginang printer developed by Priyanto is capable of producing rengginang quickly and in much larger quantities. This tool can double the printing capacity compared to manual printing. In every minute, one worker can produce 4-5 pieces of rengginang or around 240-300 rengginang per hour. Meanwhile, manually, each worker can only produce 2 rengginang per minute or 120 renggiang per hour. “The printing capacity is at least 50 kg every day. With this tool, from 1 kilogram of ingredients, steamed glutinous rice, about 110-120 pieces of rengginang can be produced,” he said.
Priyanto revealed that the tool he developed is practical and can be operated by anyone, including novice workers or those who are not experts. Unlike the manual printing process, which cannot be done by every worker because it requires high expertise and skills. This tool can print rengginang with the same size and texture specifications. “In the manual printing process, the amount of pressure during printing is sometimes different for each person, so the impact is that when fried or packaged, the rengginang is easily damaged or destroyed. With this printing tool, the pressure generated will be the same so that the rengginang is more compact, not easily destroyed, and has a neater shape,” he explained.
Besides being easy to use, this tool is also able to save production costs because it is operated without electricity or fuel. Priyanto explained that the working principle of the rengginang molding tool that he developed adopts the workings of a bottle cap. This tool consists of a body/skeleton made of cast iron, a pole made of iron axles, a wooden press, a handle to press the printed rengginang, a table to stand the tool, and a wooden printing board containing pieces of pipe.
To make glutinous rice rengginang that has been steamed is filled in the mold in the printer board. Then pressing/solidifying the rengginang is done by pulling the handle so that the pressing wood drops and solidifies the rengginang in the mold. The rengginang can then be removed from the mold for drying. “Incidentally, I developed several mold shapes such as circles, rectangles, and squares. So, you just need to change the mold according to what you want the rengginang to look like,” he explains.
This rengginang molding tool has been mass-produced. One unit is marketed at Rp. 2.5 million.
This tool has been used by several SMEs, one of which is UKM Rengginang Lestari, in Tempel, Sleman, which has been using it since 2004. Sutiyem, the owner of Rengginang Lestari, said she was helped by the printing press. According to her, the printing press can increase production capacity up to two times. In the past, when using manual printing she could only produce as much as 12 kilograms every day. However, since using the printing equipment in one day she can produce up to 50 kilograms. In the past, it was quite difficult for me to deal with a large number of orders, while we could not produce that much because of the printing problem. Thank God, after using the printing equipment, we can make rengginang in much larger quantities, said Sutiyem. (UGM Public Relations/Ika)
Source : http://ugm.ac.id/id/berita/3972-dosen.ftp.kembangkan.alat.cetak.rengginang